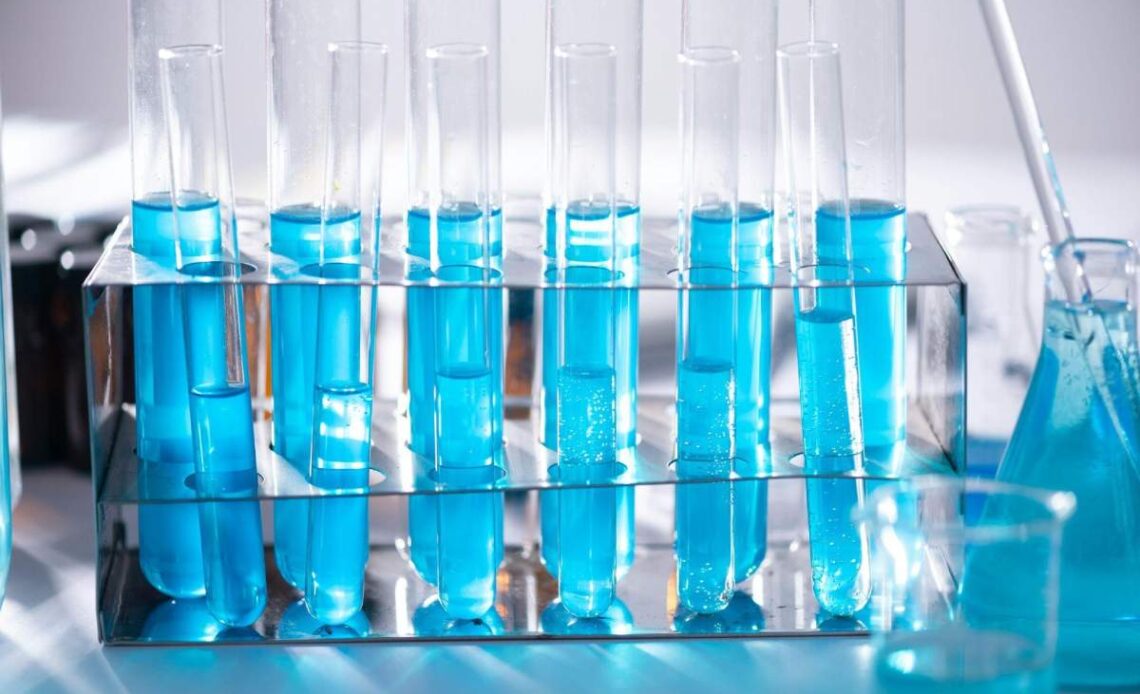
Dispensing tech is a big deal in places like electronics, pharma, and biotech—it’s the unsung hero behind getting stuff made right. Whether you’re building tiny circuits or mixing up the next big drug, precision and speed are everything. That’s where contact and non-contact dispensing come in, two different ways to plop fluids exactly where they need to go. Each has its own vibe, its own strengths and quirks, depending on what you’re trying to pull off.
Understanding Contact Dispensing
Contact dispensing is pretty hands-on—literally. The tip of the dispenser touches the surface, and out comes the fluid, thanks to some controlled pressure or a mechanical nudge. It’s a go-to for jobs where you need to nail the exact amount every time. Ever heard of picoliter dispensing? That’s one of its tricks—squeezing out teeny-tiny drops, perfect for processes like microfluidics or fancy biotech projects. It’s all about precision, which is great, but it’s not flawless. That constant touching can get messy—think contamination or gunk piling up over time.
Advantages of Contact Dispensing
Here’s why people love it: it’s dead-on accurate. If you need every drop to land just right, this is your guy. It doesn’t waste much fluid either, which is a win when you’re working with pricey stuff. The tip-to-surface action gives you tight control, especially with thick, gooey materials that’d laugh at other methods. Think gluing tiny parts together or micro-soldering—this approach has it covered. It’s reliable, and a lot of industries swear by it for that reason.
Limitations of Contact Dispensing
But it’s not all sunshine. That physical contact? Yeah, it’s a contamination magnet. Delicate surfaces can get scratched up, and after a while, the tip might clog or wear out, throwing off your flow. You’ve got to stay on top of cleaning and maintenance, which can be a hassle. And if you’re dealing with super-small volumes, good luck—things can get finicky fast. It’s solid, but it’s got its headaches.
Understanding Non-Contact Dispensing
Now, non-contact dispensing flips the script. No touching allowed here—the fluid shoots out using air pressure, a piezoelectric zap, or even a little heat. It’s fast, it’s clean, and it’s perfect for jobs where speed and precision need to play nice. No contact means less mess, so it’s a lifesaver for fragile surfaces or uneven spots. When the old-school way just won’t cut it, this is the one to call in.
Advantages of Non-Contact Dispensing
This method’s got some serious perks. For one, it’s quick—great for cranking out tons of work in no time. No tip grinding against anything means less wear and tear, so you’re not constantly fixing stuff. It shines in high-stakes fields like semiconductors or drug-making, where contamination’s a dealbreaker. Plus, it can handle sensitive materials without breaking a sweat. If you need to zip through a job without leaving a trace, non-contact’s your friend.
Limitations of Non-Contact Dispensing
It’s not perfect, though. Precision can take a hit if a breeze sneaks in or something throws off the jetting. Some fluids are picky—they need just the right mix to fly straight. And when you’re going fast, droplet sizes might wobble a bit, which isn’t ideal. Thick, sticky stuff? Forget it—this method struggles there. Setup’s a bit of a puzzle too; you’ve got to dial it in just right, and the gear can cost a pretty penny compared to the contact route.
Choosing the Right Dispensing Method
So, which one wins? Depends on what you’re up to. Thick fluids and pinpoint accuracy? Contact’s your pick. Need speed and a no-mess guarantee? Non-contact’s calling your name. It’s all about the details—how viscous your stuff is, how perfect it’s gotta be, and whether contamination keeps you up at night. Smart companies weigh the pros and cons, poke around their setup, and figure out what fits. Cost, speed, reliability—it’s a balancing act, and there’s no one-size-fits-all answer.
Conclusion
Contact and non-contact dispensing are like two sides of a coin—both awesome, both flawed. Contact brings the control and accuracy but drags along some contamination baggage. Non-contact’s fast and flexible, though it needs a steady hand to keep it on point. Knowing what each brings to the table helps industries fine-tune their game. The tech’s only getting better, too—smarter tweaks and innovations are pushing both methods to new heights. Down the road, that means slicker processes, tighter results, and maybe even a few more breakthroughs worth bragging about.
Also Read: Why Is Outsourcing to CROs a Cost-Effective Solution for Mid-Size Biotech Organizations?